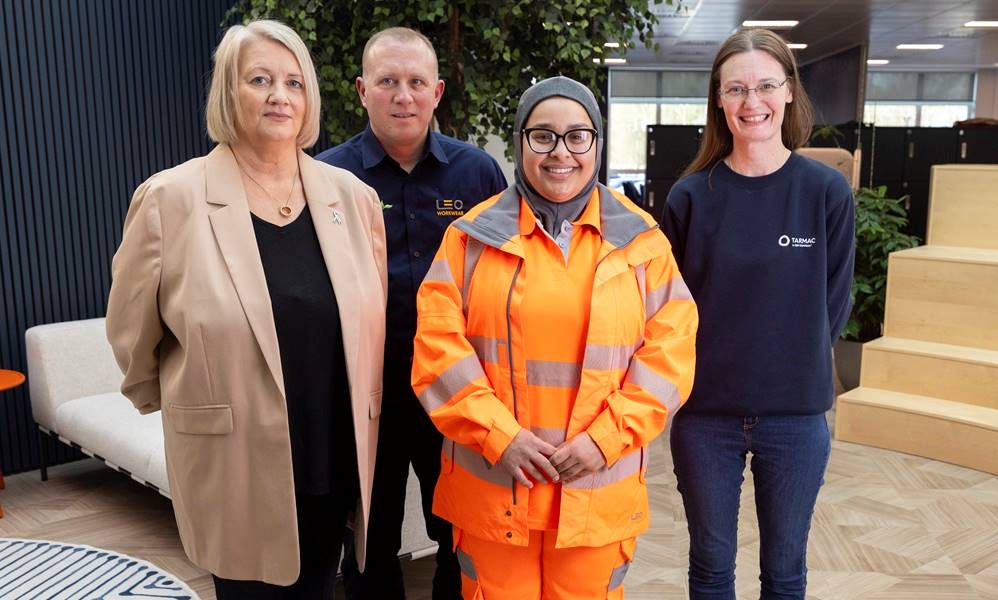
Tarmac has played a key role in developing and launching a new PPE hijab, now available from workwear supplier Leo. Designed in collaboration with Tarmac’s Sustainability Graduate, Amall Saleh, the product enhances comfort, safety, and inclusivity for women in construction.
Tarmac’s Female Voice network has been working with suppliers to improve PPE options for women across the business. As a sustainability construction advisor and hijab wearer, Amall was invited to support product testing and share her insights.
Amall said: “Before this, I had to adapt my hijab to fit existing PPE, often making compromises. It never occurred to me that a solution could be designed specifically with my needs in mind while also meeting health and safety standards.”
The PPE hijab was developed through a three-stage design process, with Amall and the Tarmac team working closely with Leo to refine the product. A key innovation is the ‘halo band’, a fabric band around the crown that secures a hard hat without pulling on the hair.
Tarmac worked with its trusted PPE supplier, Arco, to support the development of the hijab alongside Leo. Arco has been a long-standing partner in Tarmac’s PPE journey, playing a crucial role in ensuring inclusive and high-quality protective workwear is available across the business. Their collaboration has helped drive improvements in PPE for all colleagues, including maternity wear and wider range of materials and sizes.
Amall added: “When I received the prototype with the halo band, I was so excited. I even asked my mum to try on the smaller version! Seeing my feedback shape the final product was incredible, and I now feel much more comfortable on-site.”
Kirsten Kobrin, Category Manager FM&E, emphasised the wider impact of inclusive PPE: “When I started, none of the PPE I was given fit me, so I made it my mission to improve the range. Now, we offer maternity PPE, different sizes and materials, and now, the PPE hijab.”
Luke Alcock, Sales Director at Leo Workwear, added “At Leo, we believe everyone deserves workwear that enables them to do their job safely and comfortably. We achieve this by working directly with those who face these challenges every day. Combining Amall’s real-world experience with our expertise in workwear design has resulted in an excellent product that will support many women facing the same issues. We’re committed to offering and stocking inclusive PPE because it’s the right thing to do, not just to cater for the mass-market. Our goal is to ensure that everyone has access to the protective clothing they need to stay safe at work.”
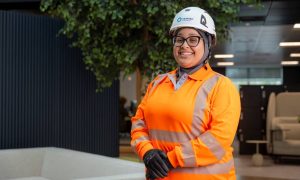
Heather Sperry, National Account Manager at Arco, said: “At Arco we are proud to have supported Tarmac and Leo Workwear in developing this innovative PPE hijab. As a longstanding PPE partner to Tarmac, we’ve worked together for many years to ensure that all colleagues have access to high-quality protective workwear that meets their specific needs. The hijab’s thoughtful design reflects Leo Workwear’s willingness to listen and respond to feedback from Tarmac and Amall, ensuring the final product meets both practical and cultural requirements.
“The inclusion of the ‘halo band’ is a great example of how collaboration and real-world insights can drive meaningful improvements in PPE design. This project reflects our ongoing mission to improve inclusivity and comfort in workwear and we’re delighted to see the positive impact this product will have on women in construction. By working closely with Amall, Tarmac, and Leo Workwear, we’ve helped create a solution that not only enhances safety but also empowers individuals to feel confident and comfortable on site.”
Now available to Tarmac colleagues, the PPE hijab marks a significant step in ensuring workwear is inclusive and empowering. Its availability to the wider industry will help drive greater diversity across the construction sector.
Source – Tarmac